Alcon Johor’s New AI-Based Decision Support System – Improving Productivity and Saving Costs
- UM Research
- Jun 15, 2023
- 2 min read
Updated: Nov 2, 2023
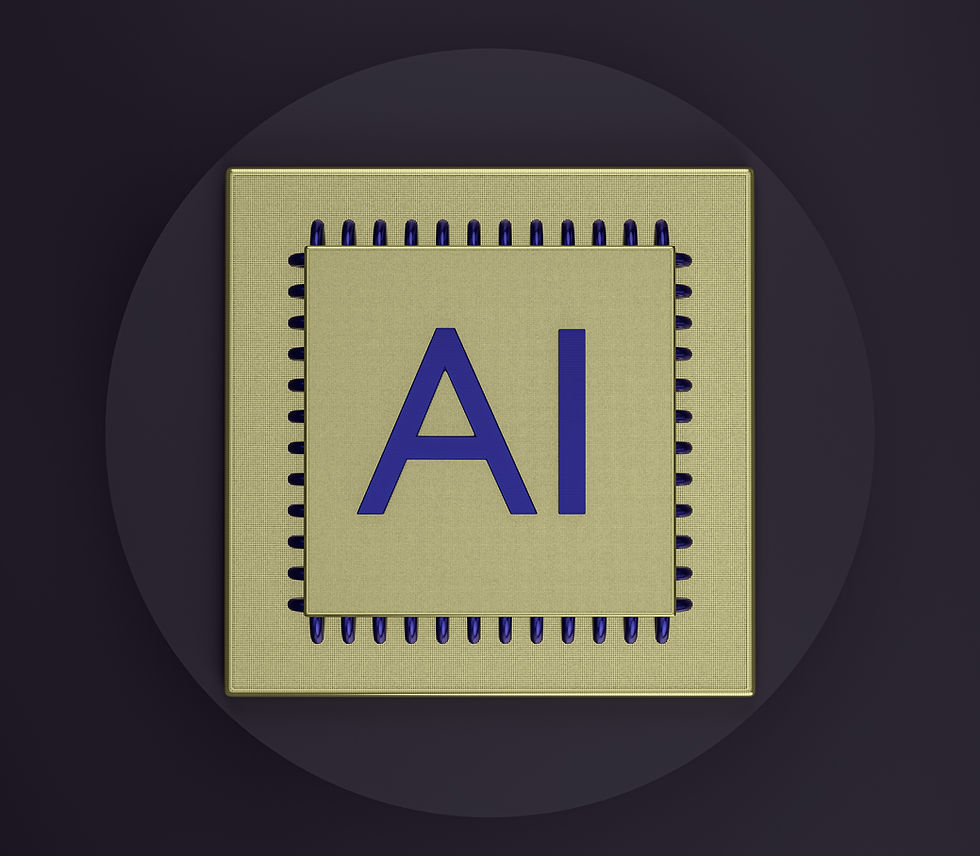
Alcon Johor aims to expand and improve on its contact lens production through the introduction of an AI-based Decision Support System (DSS). This system will provide a set of recommendations based on past data and results, providing better prediction and reduced targeting duration. Alcon plans to roll out this system to every other molding lines, contributing to the company’s plans to automate its manufacturing line in the future.
Alcon Johor is a branch of the Alcon company (which produces a wide range of vision care products from eye drops to complex surgical equipment) located at Pelabuhan Tanjung Pelepas Johor. This branch specializes in manufacturing contact lenses for refractive error correction and bandage lens, with a production magnitude of over a thousand lenses per month.
In this company, quality control and the targeting process are both vital prerequisites. The current quality control being used, however, will only allow a small margin of error to produce the highest-quality products for the customers. As measurement errors accumulate, more and more products will be rejected, severely impacting the manufacturing costs. Likewise, the targeting process is required for the precise moulding of the single-use moulds. The current targeting process, unfortunately, takes a long time to finish incurring greater productivity losses. Furthermore, because this manual process requires human judgement, it is thus prone to error which will severely impact the production line’s capacity to fulfil customer demands.
To rectify this issue, Alcon Johor plans to introduce an artificial intelligence (AI)-based Decision Support System (DSS) in three phases. This system will provide a set of recommendations provided by its machine-learning model based on past production data and results. These recommendations will be referred to by the technicians when preparing the tools, which in turn will then be fed into the lens moulders to produce the predicted target values.

Figure 1 :
Diagram illustrating the high-level moulding and production steps; DSS components are highlighted in blue while the research component (focusing on the model learner and analyser) is highlighted in the red dotted line.
AI has contributed greatly to improving business productivity and cost-savings for Alcon Johor. With the full implementation of DSS, it is expected to reduce the targeting duration by more than 20%-30% and provide better prediction of the intended power for production.
The success of DSS Phase 1 has paved the way for the model to be rolled out to other moulders in the company for Phase 2. DSS Phase 2 will also include a new AI model and recommendation for another Alcon product, which will be able to leverage the DSS for lesser manufacturing errors and optimum production time. This project will be continued for Phase 3 to cover the entire manufacturing lines in Alcon Johor.
With the implementation of the DSS, Alcon’s target of modernizing its production and manufacturing will become closer to reality, in line with the company’s vision to realize data-driven and highly-automated manufacturing processes capable of enhancing eye-care product production and quickly meeting consumers’ demands while simultaneously reducing manufacturing costs.
Author and researcher featured:
Prof. Dr. Loo Chu Kiong
Department of Artificial Intelligence
Faculty of Computer Science and Information Technology
Copyedit: Michael Hoe Guang Jian (michaelhoe.hoe@gmail.com)
Comments